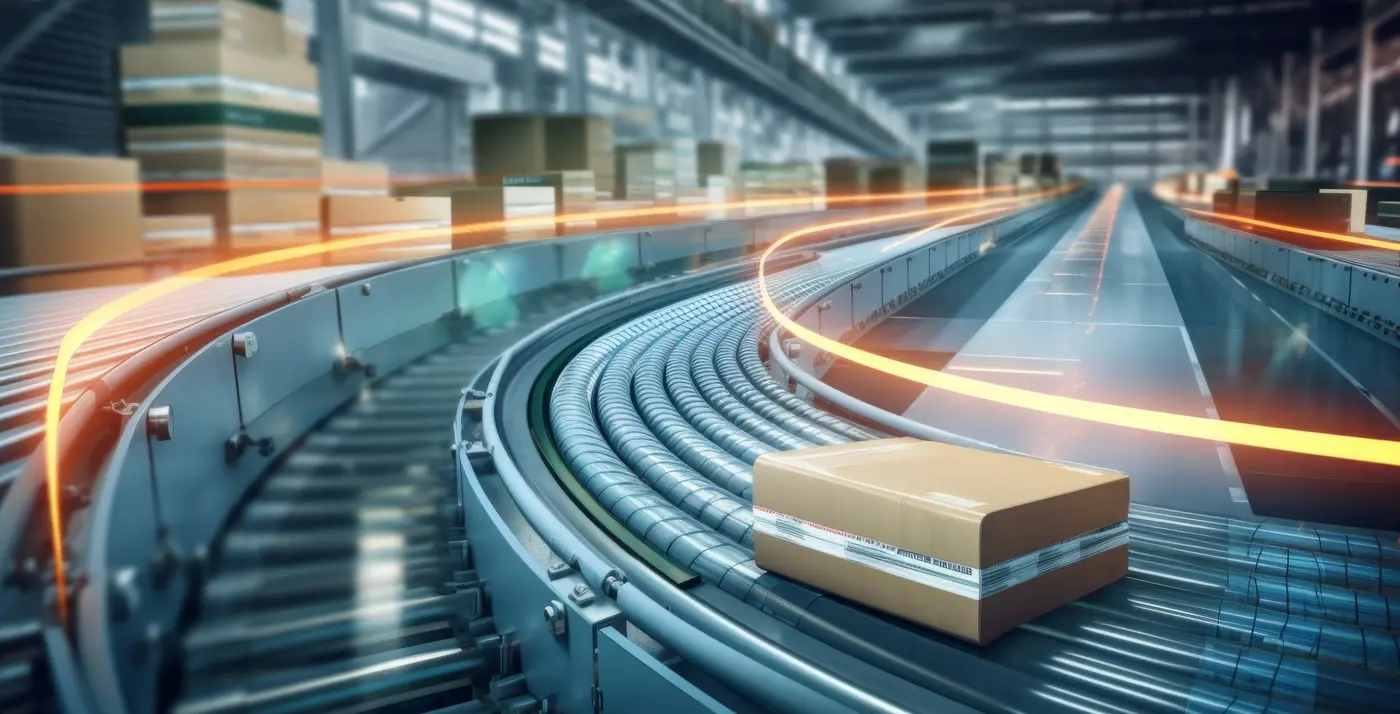
8. 2. 2024
What does the Just In Time (JIT) method mean?
JIT stands for Just In Time. It represents an approach to managing production processes that focuses on minimizing inventory and optimizing time. It aims to deliver products or services precisely on time, thereby eliminating costs associated with storing excess inventory. The Just In Time production method has its origins in the Japanese automotive industry; particularly at Toyota where it was developed during the 20th century. Japanese automakers used it to overcome resource constraints after World War II and to optimize their production processes. The method was later adopted in many other industries around the world.
Demand-driven production and minimum stocks
Just In Time production is driven by actual customer demand. Instead of producing large batches for stock, smaller batches or individual pieces are prepared in quantities that are actually needed. This increases companies’ ability to respond to rapidly changing market conditions and consumer preferences while eliminating the amount of raw materials, supplies, work-in-progress and finished goods that must be held in stock. This enables businesses to optimise use of warehouse space, thus reducing associated costs such as space rental and maintenance, utilities and security, and insurance.
All these aspects also influence demand for storage space and logistics facilities. "Whereas companies used to rent warehouses even when they had no specific use for them and thus maximised the rented space, today, in connection with production optimization, we can also see a push for efficiency in the area of warehouse space. Companies are downsizing their spaces, trying to negotiate leases for periods shorter than 5 years, and demanding smaller and easily accessible spaces," explains Miroslav Kotek, Director of Industrial Real Estate at Colliers.
Production flexibility and challenges and a look to the future
A key element of the Just In Time method is the ability to react quickly to changes in production or demand. Flexibility is achieved by reducing the amount of specialized equipment used, deploying a workforce capable of performing different tasks, and using flexible production lines that allow for rapid retooling. This enables companies to switch easily between production programmes and respond to changes in demand. However, flexibility in manufacturing is not limited to a company's internal processes. Cooperation with suppliers is also important. Everything is geared towards enabling companies to introduce new products or adapt existing products more quickly to meet customer expectations.
Using a Just In Time approach also brings with it some risks and challenges that companies need to take into account. Just In Time operations require well-trained staff who are able to react quickly to changes in processes. This is not easy to manage in times of very low unemployment and higher employee turnover. A manufacturer is also highly dependent on its supply chain and interruptions in the supply of parts or raw materials can negatively affect or even completely stop production. The increased risk of production disruptions is mainly due to minimal inventories. This was evident, for example, during the pandemic when various trade and transport restrictions interrupted supplies while there was no stock to cover the disruption.
With the advent of modern technology, companies are increasingly able to implement Just In Time. Auto-ID systems, IoT (Internet of Things) and software platforms enable detailed tracking of inventory movements in real time. This leads to better demand tracking, more efficient supply chain management, and faster response to market changes. Just In Time will continue to play a key role in optimizing production in the future. And thus also in warehouse optimization. If these are issues you are dealing with, do not hesitate to contact our experts.